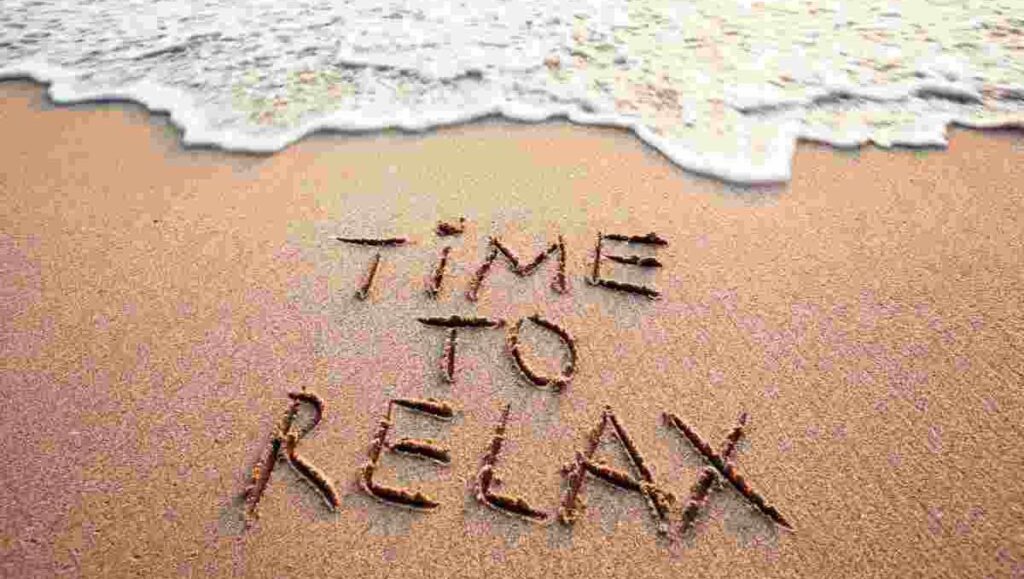
Following on from our previous post on the topic, here’s a step-by-step guide to show you how to implement the process approach.
How to implement the process approach
1. Start at the top
Getting your team to embrace the process approach starts with YOU
Do you like the sound of having more time to focus on the work you enjoy most instead of a disparate array of management responsibilities? Then it’s time to get serious about fully implementing the process approach.
In case you missed our last post, the process approach is a revolutionary management strategy where every single process in an organisation is frequently reviewed and given a clearly defined purpose that relates to other processes in the organisation. In other words, it guards against inertia ensuring that all of your systems are feeding into each other and working well together.
The result? Better output, happy customers, engaged staff and business gains. But let’s rewind this scenario because none of that is going to happen without the 100 per cent commitment of one key individual at the outset.
Managers must take the time to evaluate, review and update processes, as well as engage others in doing so. It might seem counter-intuitive, but it is a fact that the more engaged senior management is in the quality system, the more freedom they have to walk away. Why?
Cultural change begins with key decision-makers who are the link between departments, the ones to invest in training or call interdepartmental meetings.
If you are a manager, you are the figurehead who sets the tone of the organisation.
Working in competitive and rigorously-regulated fields, laboratories must find smarter ways of doing things and doing them well. And they must do so exponentially, year after year.
In order to set your business up for long-term success and to ensure it doesn’t fall behind or stagnate, you have to bake excellence and continual improvement into all of your operations. A best-practice, business-savvy quality system won’t happen by accident or from the bottom up.
If you communicate your organisational vision and quality system well, your staff will also communicate with each other well. It is a virtuous cycle – one that may in turn help you refine your vision and open you up to new fields of testing and service areas.
If you truly embrace the process approach (and the powerful Plan-Do-Check-Act cycle) and embed it into every level of the organisation, continual improvement will take care of itself.
Talk to your staff in terms of processes, measures, inputs and outputs and ask for all documentation to be presented in process format. Use flowcharts to show how processes link together and engage your staff in making sure these are correct. Talk about why a process exists – what it is supposed to achieve.
Weave the process approach into every day, combine it with continual improvement, and your team will be on quality-system cruise control.
You’ll have staff suggesting efficiencies and pointing out risks and opportunities not just for compliance’s sake, but because they are intrinsically motivated towards continual improvement and understand the rationale behind all of your laboratory processes.
2. Take a closer look at the purpose of accreditation and recent ISO changes.
Once you have the fundamentals of the process approach and continual improvement in place you are ready to really reap the benefits of accreditation.
To understand how to go about gearing the process approach towards long-term success for your laboratory, it helps to take a close look at new requirements around risk and opportunity.
Continual improvement and operational excellence are not just about complying with the bare minimum requirements of ISO’s increased emphasis on risk-based thinking.
By making the continual assessment of risk and opportunity central to your operations, the ISO standards are setting you up to become more efficient and competitive as a business (now and in the future).
The fact is businesses need to remain efficient in the face of 21st-century challenges such as increased competition, new technology, and higher customer expectations. The new requirements are a recognition of this.
So bear in mind, when it comes to complying with the risk-based thinking requirement, the process approach is your friend. Don’t be intimidated! Having a clear view of your key processes makes it so much easier to identify opportunities and risks. This is where things get exciting from a business point of view.
Managing risk effectively while always seeking opportunities will actually enable you to take risks and chase bigger goals – whether that’s for your organisation and team (moving into new service areas and fields for instance) or for you personally in your life (think more holidays, earlier retirement!).
3. Tailor how you meet requirements.
Develop your own approach to risk-based thinking for the purpose of bigger goals (not just compliance)
How strategically you meet the requirements of the new ISO standards is up to you.
Perhaps your organisation is already well within the bounds of what NATA expects you to be doing (as a bare minimum) regarding the process approach and risk-based thinking.
But as the new standard also provides increased autonomy in the amount of documentation you use to meet these requirements, it really is up to you how fully you embrace the opportunity. You don’t need to write long involved procedures to meet these requirements – it’s about thinking and designing in a process-orientated way and ensuring that risks and opportunities are considered and taken into account.
Placing the process approach at the heart of your systems with risk-based thinking will unlock a new level of freedom in your role.
It will also provide career development and fulfilment for your staff, and this will flow back to your business, customers, and again, YOU. You’ve worked hard to get your organisation to this point. Don’t you want the peace of mind of being able to delegate and reduce your own mental clutter, and the freedom to grow or sell your business if you desire?
4. Make yourself more or less replaceable
(Your business will flourish!)
One of the key purposes of having a defined quality system is that it doesn’t depend on just one person.
Instead of holding all the pieces of the puzzle, unable to step aside in case it all falls apart, ensure the processes that make up your laboratory slot together without constant oversight.
With a manager-led improvement culture (based on the process approach), your quality system will become highly valued by your team.
Silos between departments will be broken down, ensuring everyone is continually kept on the same page about organisational processes.
Your quality system then becomes a dynamic, defining and tangible part of your organisation, not just words in a quality manual. That way you can leave the organisation in the safe hands of your staff and your system, and maybe even take that long overdue email-free holiday.
Here are those details again in a printable PDF for those of you who like visual reminders. Click here for a downloadable copy.
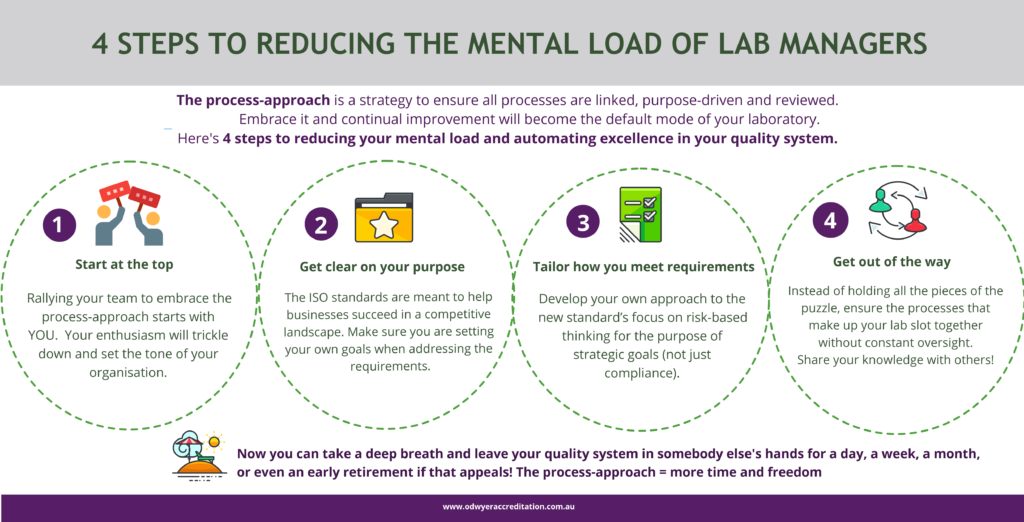
Get support
We help managers and teams implement all of the above and more. The time involved in establishing the process-approach throughout your organisation is often less than managers expect. However, without a dedicated day or team member to do this critical work, the day-to-day takes over and plans for improvement are shelved.
Check out our courses and consulting services below if you or your staff require extra facilitation to implement the process approach and improve your quality system.
The Best-Practice Internal Audit Program Your Lab Needs
Or sign up to our email list for regular tips and insights about how to ensure your accreditation is serving your business goals.