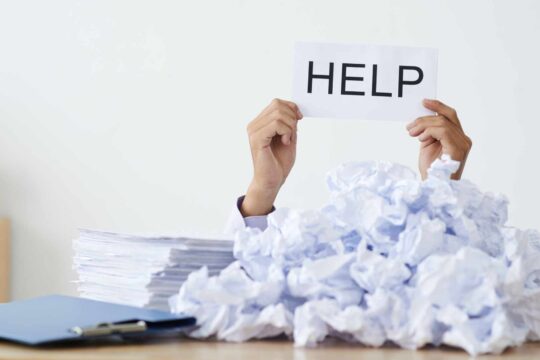
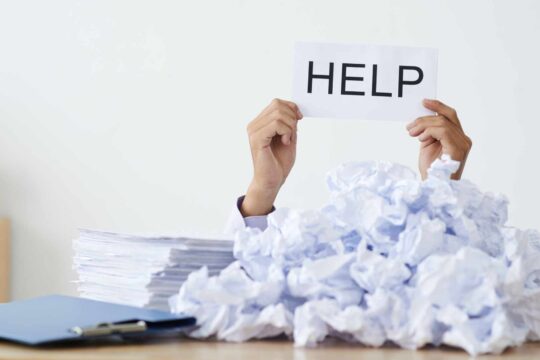
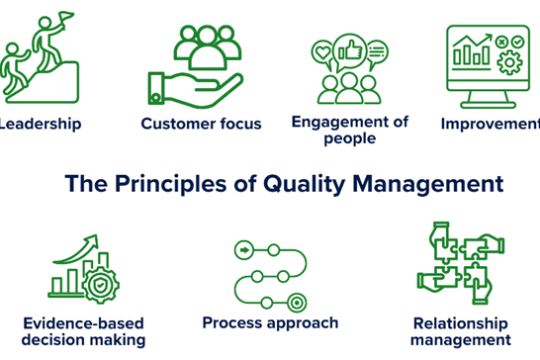
What is Quality in laboratories all about?
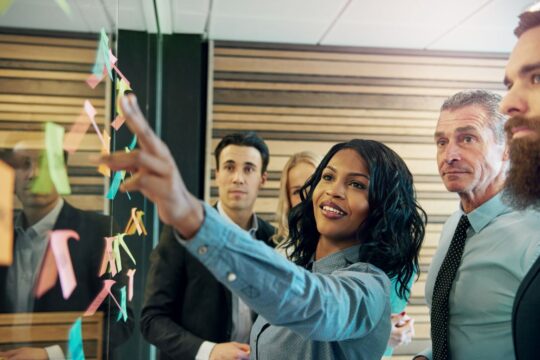
The 5 Deadly Sins of Quality and Compliance
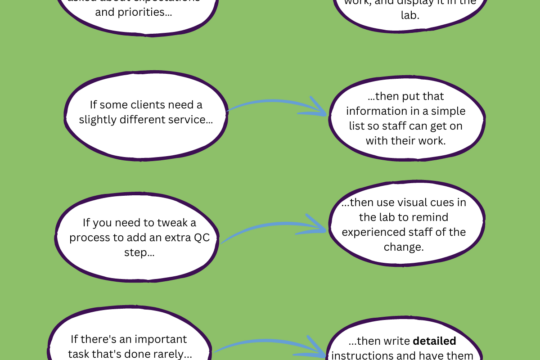
What’s the point of the Quality Management System?
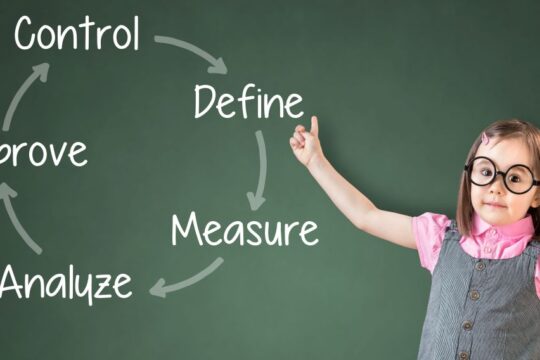
Internal audit planning: How a selective focus helps you get more from your quality systems
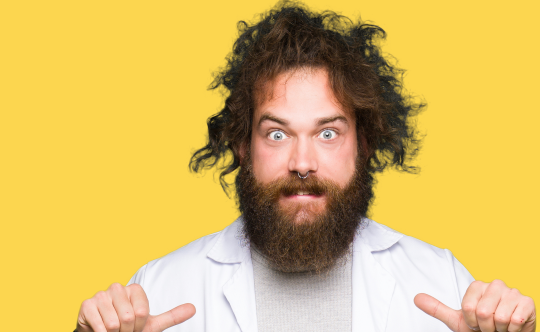
8 simple ways to make your next NATA assessment successful AND stress-free
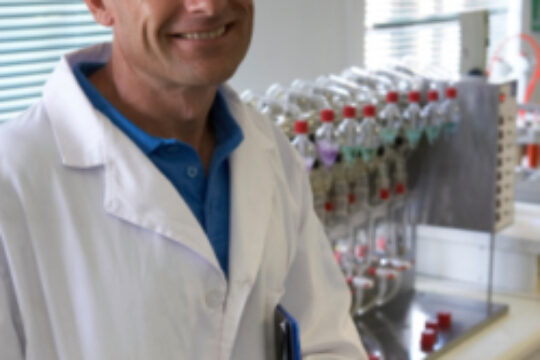
3 pro tips for creating a successful internal audit schedule and program
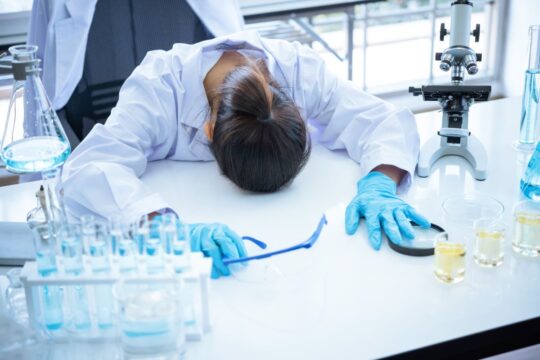
5 simple steps for writing user-friendly lab management documents
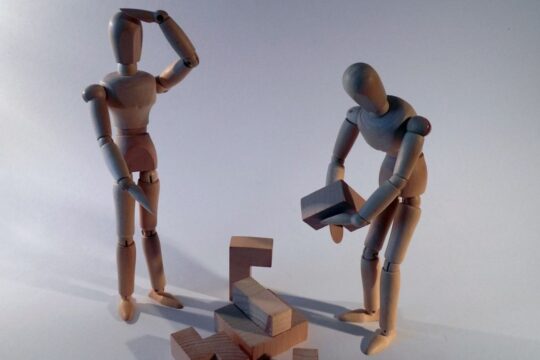
Understanding NATA assessments and how to best respond to your report
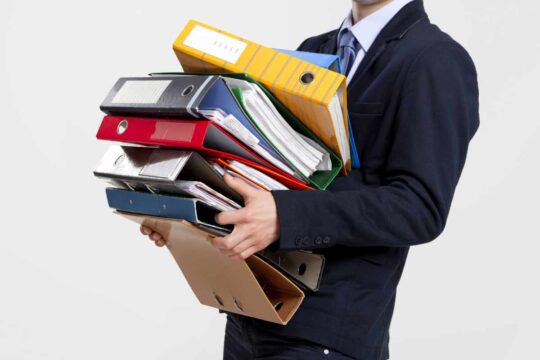
How to write great SOPs and declutter lab systems
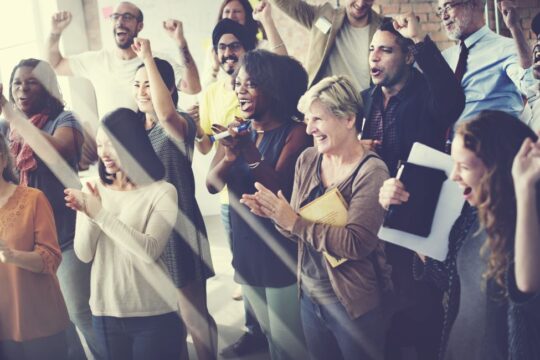
You’ve got NATA Accreditation – what comes next?
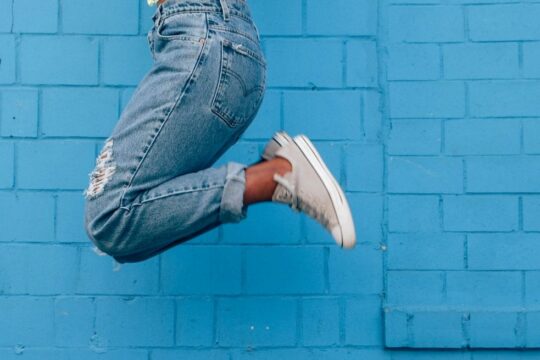
A minimum viable audit program
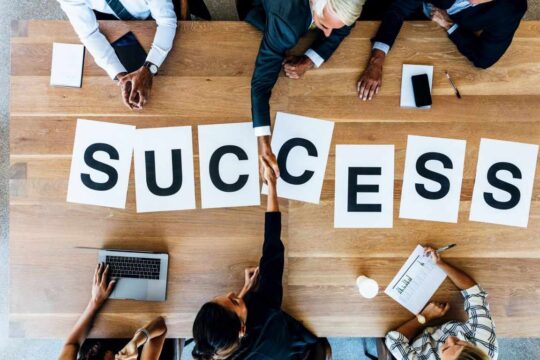
The six pillars of a successful NATA application
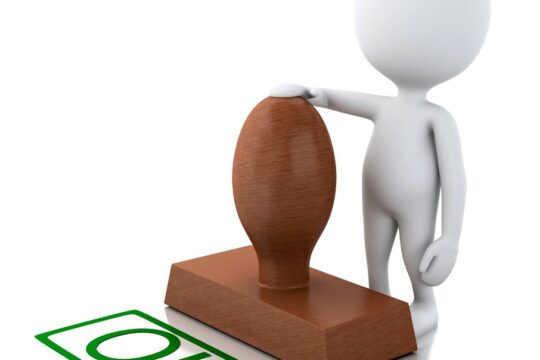
Save time and money on NATA requirements with 5 strategic steps.
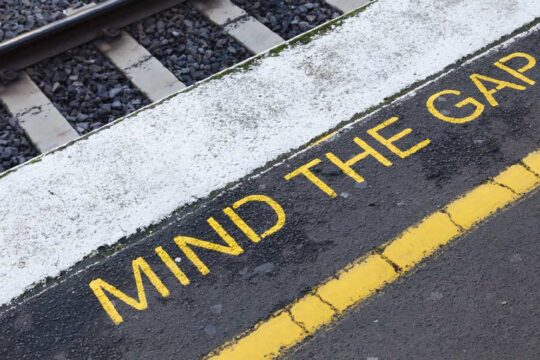