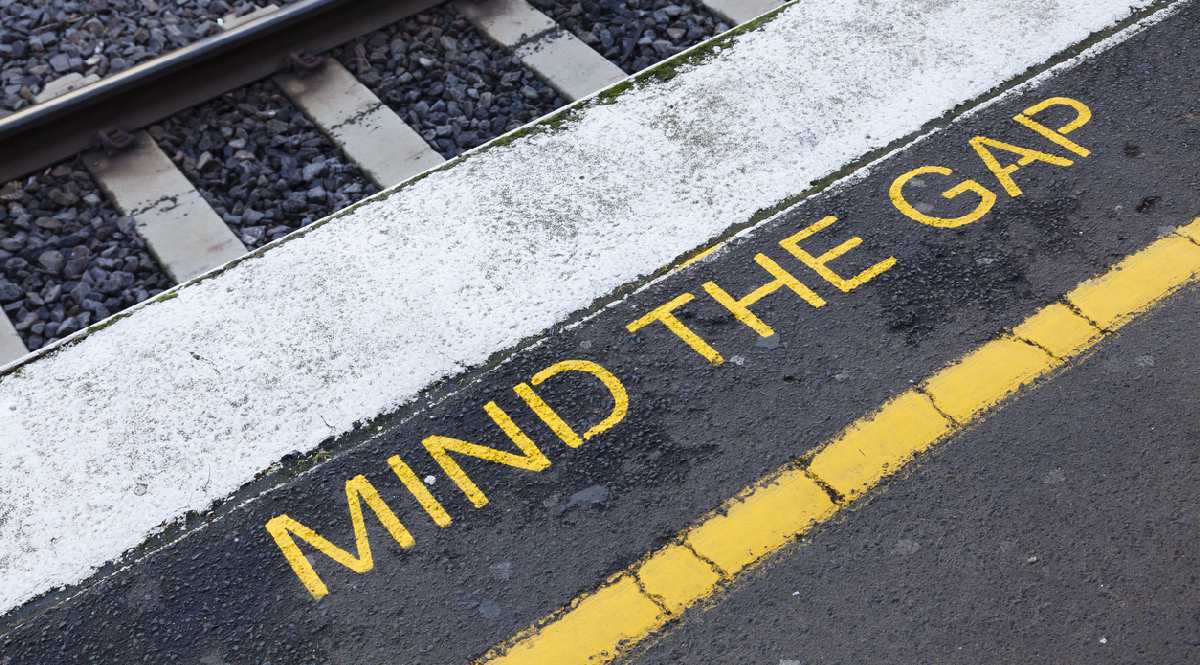
Cover all your bases with NATA and educate your staff with a gap analysis.
You’ve had your quality system documents in place for years now, and you made sure they met NATA’s requirements at the beginning. But NATA keeps suggesting or even requiring more changes to the system. So you start adding extra bits and pieces all over the place, or additional procedures, as you prepare to send a response to NATA. What you really need is a gap analysis.
Because the truth is, no matter how hard you work on your responses, you can still end up getting unnecessary NATA non-conformances just because you’re not clear about where or how your quality system addresses some elements of the standard. This can happen when new staff join the quality or management team, if the system was developed by outside help, or you (or the staff) have simply looked at your documents too often and can’t see the wood for the trees.
Do you want to waste all the time and money you’ve invested in developing that system by adding unnecessary extra procedures and ending up with a hotchpotch of overlapping documents? Of course you don’t.
So, what’s the solution? Is it best to write your quality manual according to the clauses in the standard? Wrong! Please don’t do that. Each organisation is so different that there isn’t relatable content for each clause of the new standards.
But how can you be sure you’ve covered everything and avoid that problem of NATA deciding you need a new procedure? A gap analysis is the way to go. Develop a gap analysis versus the standard you are working to and keep it as a controlled document. Update it each time you make changes to your management system.
Go ahead and structure your manual and procedures according to your business processes. Group them under headings that make sense to you. That way, they will also make sense to your staff and serve as a valuable reference for the “right” way to run things, both for NATA compliance and your organisation. Use a gap analysis to avoid doubling up on procedures and as a helpful tool for demonstrating to NATA how your system covers the requirements.
Why a gap analysis
Having a gap analysis means you have a document to refer to when NATA says, “You haven’t covered x in your system.” Instead of writing additional documents to keep NATA happy (which you will then have to update regularly), a detailed gap analysis explains HOW your current processes meet the requirements. It’s incredibly useful in situations when you have a team of people speaking with NATA during the assessment, some of whom may not realise how (or where in your documents) the organisation addresses some criteria.
How to do a gap analysis
One of the biggest mistakes that quality practitioners make is to assume that they know everything about the quality system and how it addresses various elements of the applicable standard. This is why, in my experience, developing a gap analysis should include people outside of the quality circle. The steps:
- Make a table based on the standard you need to meet. It will be very long but avoid the temptation to abbreviate the text too much as your interpretation may completely miss someone else’s point.
- Fill out the details with columns for how we meet this, document reference, gaps identified, notes and actions.
- Unless there’s no help in sight, don’t do this on your own. Get the team together, whether it’s your senior scientists, quality team, medical director or a family member. Now is the time to get all the different viewpoints on how your organisation meets the standard.
- Ask everyone to do some brainstorming (this could be just jotting down what comes to mind without looking up specific documents) and bring their ideas along to the first session.
- Start running regular sessions and put down all the different ways that you meet the requirements. Write down document references, if relevant.
- You will need at least three sessions to complete this, and it could take considerably more if you have a big, engaged team!
NOTE: You do NOT need a document reference for every clause.
With the recent changes to process-based standards for ISO 9001 and ISO 17025 and, eventually, ISO 15189, there are now more clauses for which you don’t have to write a procedure. As I’ve been saying for years, it’s more important to do quality than to write about it. Labs that have structured their quality manual to align with the numbering in ISO17025 or ISO15189 find it increasingly difficult to write something that makes sense in their context.
How to use the gap analysis
There are a few different situations where this gap analysis really comes into its own:
Before the assessment
Use the GAP analysis to educate and inform your staff members. Concentrate on the sections they may have to answer questions about in their role.
During the NATA assessment
If you’re unsure if you are giving NATA the answers they’re looking for, ask them to tell you which clause of the standard they are on and then look up the gap analysis. You will be so glad you did the gap analysis at this point!
After the assessment
Check all of the system-related non-conformances in the assessment report versus the GAP analysis. You may find that you have already covered their concerns in your system.
The time it takes to do a GAP analysis is absolutely worth it. You and your team will feel prepared and even excited to talk about how your organisation meets the requirements. It will show NATA that you really have done your homework, and at the same time, it will help you understand what your lab already does well, what it can do better, and how you can get to where you want to be.
If you would like help pulling your gap analysis together, get in touch. There’s nothing we enjoy more than enabling people to run their systems better!